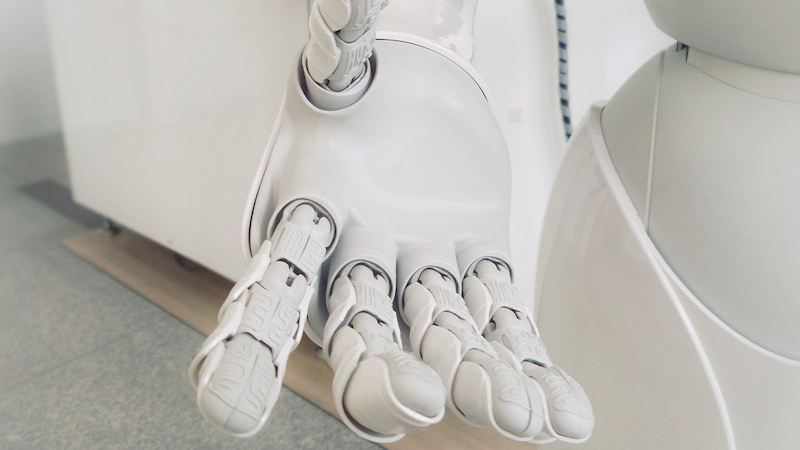
Experts expected the labor deficit to persist for several years, regardless of job openings in the United States. As a result, businesses, particularly the auto industry, turned to automation as a solution to the ongoing labor shortage. In turn, the machine-made industry continued to grow. Orders for automated and robotic technologies increased by 40% in the first quarter of 2022, compared to a 21% increase in the previous quarter.
Michael Cicco, CEO of industrial robot provider Fanuc America, mentioned that robots were becoming easier to operate. They were not like what companies used to think: complex or expensive to execute. However, the increased use of automated technology has become a worry for many. The reason was the displacement of human employees in the future. CEO Cico and MIT economics professor Daron Acemoglu had a similar outlook on the consequences of the rise of automation. He also stated that the labor shortage was just temporary.
Many industries and countries have jumped on the automation and robotic trend. It boosts a company’s productivity and efficiency. Labor costs are reduced when robots can take over ordinary jobs. It aids firms in keeping their operations running during a crisis. Such crises include the “anti-work movement,” COVID-19, and Biden’s plan for unemployment. Others include individuals who lack the skill set for certain jobs and those who are seeking or not seeking work. Those who have a job may search for other jobs with better salaries and benefits or jobs related to their field to find meaning in their job and to provide for their family.
Many of these crises contribute to the demand for automation and robotics in many industries to solve the shortage of workers. Hospitals, retail, and food delivery are examples. Uber Eats introduced an EV and a sidewalk robot to deliver food to customers (I talk about this in my other article). Daily Mail reported that FamilyMart, a Japanese corner store chain, used a 7-foot robot, Model-T, which is controlled by human operators, for stocking items on the shelves. It assisted in alleviating Japan’s labor crisis by allowing employees to avoid direct contact with others within a safe distance during a pandemic.
Yes, more robots are entering the workplace, but they are not replacing human employees. How can they replace humans? Humans design robots and understand how to deactivate, maintain, repair, and fix them if they break down. They’re there to figure out how to keep robotic systems safe from hackers. Furthermore, while robots are learning and performing tasks that humans can do, there is still a long way to go in terms of creativity, innovation, and invention. As a result, humans are needed in the workforce. Robots are there to do repetitive tasks to reduce employees’ burden of doing extra work when there are not enough workers, as Moxi assists nurses. They are also there to help employees focus on other tasks or learn new skills that robots cannot perform, such as soft skills as well as some hard skills.
Automation and robotics have dramatically increased as an alternative way to solve labor shortages, and they are not going away in the future. These technologies have benefited businesses in many ways, but that does not mean that humans will be replaced by them. Businesses still need humans to perform tasks that require both soft and hard skills. Human experts in these technologies are there to prevent hackers from getting their hands on robots and to maintain robots in good shape. They are there to develop some materials to allow robots to sense or to be able to repair themselves. They are there to train and teach them new stuff. Robots, on the other hand, are there to give a helping hand, at least the functional ones. Whatever the case may be, what does the future hold for positive human attributes and social interaction?
Sources:
Robot Orders Surge 40% as Employers Seek Relief from Labor Shortages